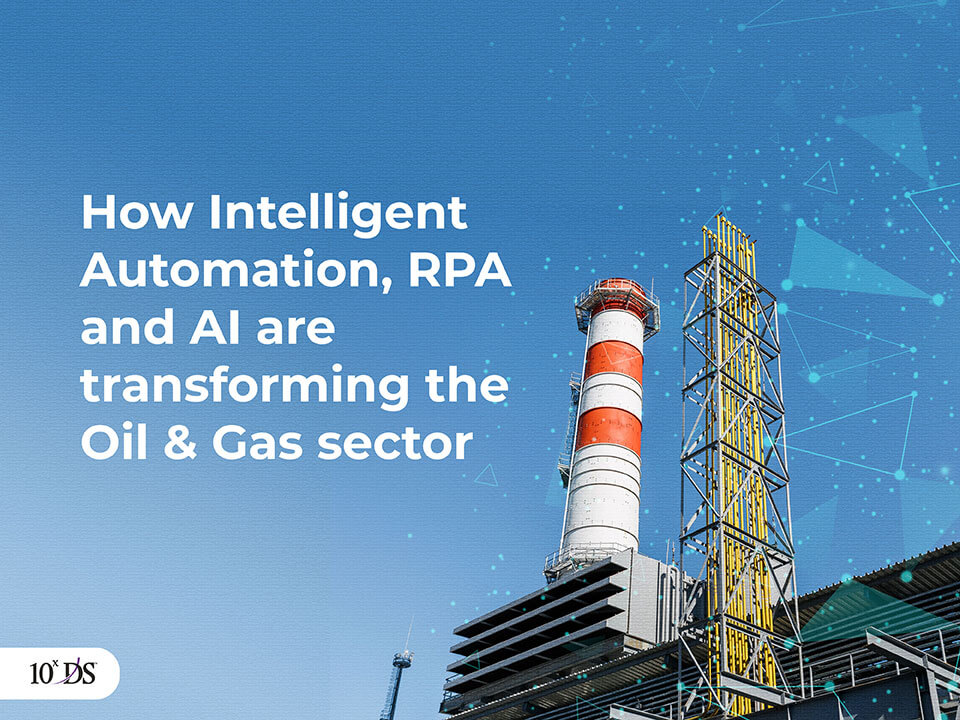
How Intelligent Automation, RPA and AI are transforming the Oil & Gas sector
Fluctuating oil prices is a major challenge faced by companies, government and common man as other industries too are directly or indirectly dependent on oil. Companies try to control costs by optimizing the operational performance. The key here is to leverage emerging technologies to increase operational efficiency in all the functions. Even though many Oil companies across the globe have embraced these latest digital transformation technologies such as Intelligent Automation (IA), Robotic Process Automation (RPA) and Artificial Intelligence (AI) for internal functions such as IT, Finance and HR, many are still reluctant to touch core oil and gas processes.
Core Oil and Gas processes are Upstream, Midstream and Downstream. ‘Upstream‘ processes deal with extracting oil and natural gas from the ground; ‘midstream‘ is about safely moving them thousands of miles; and ‘downstream‘ is converting these resources into the fuels and finished products that is ready for use.
In this blog, let’s discuss how Intelligent automation and RPA are optimising these upstream, midstream and downstream processes.
1. Upstream
a) Finding new sources of oil
Oil companies depend on data from seismic surveys for finding oil sources, but these surveys do not provide a clear picture of rock formations as underwater currents and other factors affects the images. This makes the data yielded, “noisy data”. Scientists need to analyze these rock formations which helps them locate oil deposits below the ocean floor. These surveys take human workers several months to interpret thus making the entire process slow to find sources of oil. Some Oil companies have started using machine-learning algorithms to filter out the noisy data. This Artificial Intelligence system reduces the time needed to produce clearer images bringing the search process time down to only few weeks and thus they can screen more locations very quickly to pick the best ones for drilling.
b) Field Operations
Well data resides in various legacy systems making it difficult for analysing well production and forecast availability of oil. Information from various systems need to be gathered and compiled manually to analyse production and forecast and to rank issues so that the field operations can be planned. Automating checks and alerts processes using RPA allows functional leaders to manage the process by exception. Moreover, reducing manual processes overall frees up company analysts to focus on generating data-driven insights.
Real-time data harnessed from the drill bit through sensors are analyzed using AI algorithms for geologists to chart more accurate course for the oil well and reduce drill wear-and-tear, thereby reducing operating costs.
Case Study: 10xDS AI Solution enabled Faster and Accurate Data Capturing from Construction Designs for O&G Company
2. Midstream
a) Predictive maintenance for equipment.
Malfunctions cost considerable amount of money for maintenance and also lead to downtime on distribution pipeline, valves and others. To prevent malfunctions, wired and wireless sensors are deployed to capture equipment-performance data such as the temperature and pressure of internal parts during optimal working and during past malfunctions. The data collected is fed into machine-learning algorithms trained on historical data. By learning which conditions preceded mechanical “trips,” the algorithms provide early warnings which help engineers to replace parts before malfunctions could halt operations.
b) Safetychecks
Computer vision techniques are used to identify safety risks near gas pumps and production equipment and alert operations managers to avoid catastrophic damages
3. Downstream
a) Logistics
Arranging transportation of refined oil products is a major task in logistics that involves a lot of coordination with Freight Forwarders. The shipment needs to be scheduled based on the selected Forwarder and the method of transit and other terms are agreed upon. The shipment needs to be tagged with vehicle so that goods in transit can be monitored. Software robots can be programmed to communicate with Forwarders to arrange shipment and update disparate systems with the details of the shipments so that physical arrangements can be made. The BOTs can also read scanned documents using OCR method to tag the shipment with vehicle number, route, destination and expected time of arrivals in systems so that real-time monitoring can be enabled.
b) Demand and Supply planning
With RPA, the oil companies are able to automate the process of gathering and merging the necessary information from various sources, running data cleansing tools, as well as transforming the final data into a plan. It also helps provide the necessary communication to upstream and midstream oil companies so as to plan exploration and production.
Case Study: Major O&G company streamlines Tender Management process leveraging 10xDS RPA solution
10xDS is currently involved in automating engineering and exploration processes for an Oil and Gas upstream company in Middle East. The company’s vision is to transform many corporate functions and upstream processes using exponential technologies.
Excited to know more about our IA, RPA and AI services? Talk to our Experts!