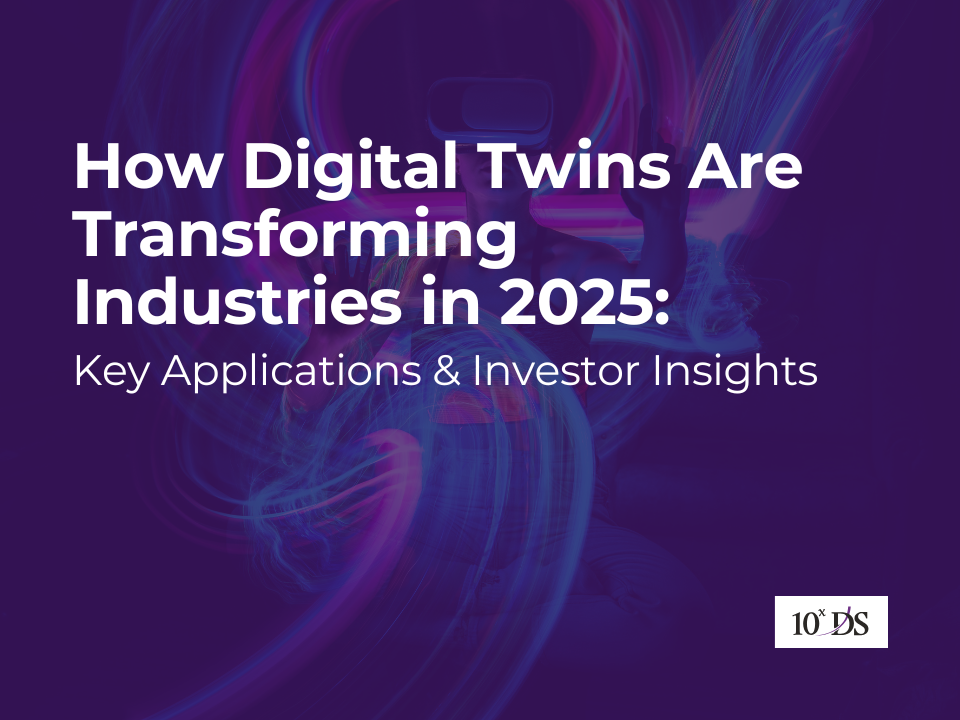
How Digital Twins Are Transforming Industries in 2025: Key Applications & Investor Insights
Introduction
As digital transformation accelerates in 2025, Digital Twin technology has emerged as a critical enabler across industries, powered by IoT, AI, and real-time data analytics.
But what exactly is a Digital Twin?
A Digital Twin is a real-time virtual replica of a physical object, system, or process. By leveraging sensor data and AI, it mirrors the behavior and performance of its real-world counterpart allowing organizations to simulate scenarios, optimize outcomes, and make informed decisions without disrupting live operations.
Among the many sectors embracing digital twins, manufacturing and industrial enterprises are leading the charge. Here’s a closer look at how this technology is transforming key operations within the sector.
1. Manufacturing & Industrial
- Predictive Maintenance of Machines and Equipment
Digital twins use sensor data from equipment (vibration, temperature, pressure, etc.) to simulate real-time conditions and predict failures before they occur. Integrated with AI/ML models and maintenance management systems, this use case helps maintenance engineers and plant managers reduce downtime, extend asset lifespan, and lower maintenance costs. - Real-Time Monitoring of Factory Floors
Using data from PLCs, SCADA, and MES systems, a factory’s digital twin mirrors real-time production activities. Edge computing enables low-latency data processing, while 3D dashboards provide visualizations for supervisors and QA teams. This results in greater production visibility, faster issue resolution, and increased overall efficiency. - Simulation & Optimization of Production Processes
Digital twins of manufacturing workflows simulate production lines and evaluate what-if scenarios to improve resource use, layout design, and operational strategies. This empowers process engineers to increase throughput, reduce waste, and react quickly to changes in demand, all while improving overall equipment effectiveness (OEE). - Digital Twin of the Product (DToP) for R&D and Performance Feedback
By creating virtual models of products using CAD and field data, companies can monitor performance, simulate real-world usage, and identify areas for design improvement. Integrated with PLM systems and AI analytics, this use case accelerates product innovation, enhances reliability, and reduces prototyping costs.
2. Healthcare
- Patient-Specific Digital Twins for Personalized Treatment Plans
Healthcare providers are now creating digital replicas of individual patients by combining genetic data, real-time vital signs, medical records, and imaging results. These personalized digital twins simulate biological processes, disease progression, and drug interactions, allowing doctors to test treatment plans virtually. By integrating AI with biomedical models, clinicians can predict how a patient may respond to different therapies, reducing trial-and-error, enabling earlier interventions, and delivering highly personalized care that improves outcomes and patient satisfaction. - Surgical Simulation and Planning
Surgeons are now using detailed 3D reconstructions of patient anatomy from MRI, CT, and ultrasound scans to create digital twins for pre-surgical planning. These virtual models, enhanced by AR/VR and haptic feedback tools, provide an immersive environment to simulate and rehearse complex procedures. With real-time physics and anatomical modelling, surgeons can accurately visualize how tissues and organs will behave during surgery, allowing them to explore different approaches, refine techniques, and anticipate complications, leading to greater precision, shorter operative times, and reduced surgical risks. - Hospital Operations Management
Beyond individual patient care, digital twins are transforming hospital operations by creating virtual replicas of entire facilities. By integrating real-time data from IoT-enabled medical devices, occupancy sensors, RFID-tagged assets, and staff tracking systems, these twins offer a comprehensive view of hospital activity. AI-driven simulation engines use this data to optimize workflows, predict patient influx, and allocate resources efficiently. As a result, administrators can better manage capacity, reduce ER wait times, improve operating room utilization, and minimize equipment downtime, leading to more streamlined operations and significant cost savings.
3. Energy & Utilities
- Digital Twins of Wind Turbines, Grids, and Power Plants
Energy providers use Digital Twins to replicate critical infrastructure such as wind turbines, grids, and power plants. Fuelled by real-time IoT data and integrated with SCADA and AI systems, these models support live performance tracking and predictive diagnostics. This allows operations teams to remotely monitor, troubleshoot, and optimize assets, ultimately reducing downtime, increasing energy output, and extending the lifespan of critical systems across both generation and distribution networks. - Load Forecasting and Asset Lifecycle Management
Digital Twins allow energy utilities to accurately forecast grid load by simulating demand and supply patterns across various scenarios. These models incorporate historical usage data, weather trends, and market dynamics to optimize load balancing and energy storage strategies. With embedded machine learning algorithms, they continuously refine predictions and detect wear patterns or potential risks to equipment health. This empowers grid operators and asset managers to make informed investment and maintenance decisions, reduce outages, and maximize infrastructure performance and returns over the asset’s lifecycle. - Environmental Impact Simulations
Digital twins help energy companies assess the environmental impact of their operations by simulating emissions, resource consumption, and ecological effects. In the renewable sector, they model factors like wind patterns, solar irradiance, and biodiversity sensitivity at potential project sites. Combined with satellite imagery, environmental datasets, and regulatory frameworks, these simulations offer a virtual testing ground for sustainability and compliance strategies. This enables sustainability teams and compliance officers to minimize project risks, ensure regulatory alignment, and strengthen ESG reporting, supporting more responsible and transparent energy development.
4. Aerospace & Defence
- Component-Level Testing in a Virtual Environment
In the aerospace and defence sectors, digital twins are widely used to simulate and test aircraft components such as engines, avionics, and landing gear under various environmental and operational conditions. These virtual models are created using detailed CAD/CAE designs, material specifications, and sensor data collected from real-world operations. By leveraging high-fidelity physics-based simulations, finite element analysis (FEA), and multi-physics modelling, engineers can accurately assess structural fatigue, thermal performance, and aerodynamic behavior without the need for physical prototypes. This approach helps design and engineering teams accelerate product development, cut down on prototyping costs, and significantly enhance safety by identifying potential issues early in the design process. - Fleet Health Management
Digital twins of entire aircraft fleets enable real-time monitoring of each unit’s health and performance by aggregating data from onboard systems, maintenance logs, environmental conditions, and flight records. Powered by AI-driven predictive analytics and anomaly detection, these digital replicas help forecast potential system failures and maintenance needs. This empowers maintenance crews and operations managers with proactive insights, resulting in increased fleet availability, reduced downtime, and optimized maintenance scheduling. - Mission Simulation
Mission-level digital twins simulate complete operational scenarios ranging from reconnaissance to combat and humanitarian response, by integrating terrain data, aircraft specifications, logistics, and threat modelling. Using advanced simulation tools, AI, and geospatial analytics, these digital environments enable real-time adjustments and outcome forecasting based on dynamic inputs. For defence strategists and mission planners, this provides a powerful platform to evaluate scenarios, optimize resource deployment, and improve mission success rates while significantly reducing the cost and risk associated with live trials.
5. Retail & Smart Spaces
- Customer Behavior Modelling
Retailers are increasingly using digital twins to model in-store customer behavior by integrating data from cameras, sensors, Wi-Fi signals, and POS systems. These virtual replicas map foot traffic, engagement zones, and dwell time, offering a clear view of how shoppers interact with the physical space. By combining AI with real-time and historical data, retailers can simulate customer journeys and tailor marketing strategies on the fly. This gives store managers and marketing teams valuable insights into consumer preferences, helping optimize product placement, drive targeted promotions, and boost both conversion rates and customer satisfaction. - Store Layout and Inventory Simulation
Digital twins of store environments enable retailers to visualize and test different layout designs, shelf arrangements, and product placements before making physical changes. They also simulate inventory flow and replenishment processes to fine-tune stocking strategies. By integrating with ERP systems, inventory management tools, and RFID data, these models offer a dynamic, real-time view of stock levels and in-store logistics. This empowers retail planners and merchandisers to reduce out-of-stock situations, enhance sales through optimized floor planning and experiment with new store concepts, all without disrupting day-to-day operations. - Facility and Logistics Optimization
In smart buildings and large-scale retail logistics centers, digital twins are deployed to optimize energy consumption, HVAC performance, space utilization, and warehouse efficiency. These models leverage real-time data from IoT-enabled infrastructure and robotics systems to mirror and manage operations dynamically. With AI algorithms predicting energy usage patterns, optimizing routes for autonomous vehicles, and identifying bottlenecks, facilities managers and supply chain leaders to reduce operational costs, enhance sustainability, and streamline logistics which are crucial advantages in today’s fast-paced, omnichannel retail environment.
These examples only scratch the surface. The transformative power of Digital Twins extends across countless other sectors from agriculture to smart cities with new applications emerging rapidly as technology evolves.
Making Digital Twins Scalable: What’s Powering the Growth
For Digital Twins to succeed at scale, they must go beyond individual assets and integrate seamlessly across enterprise ecosystems. This is now possible thanks to a powerful combination of technologies driving adoption and performance.
1. Cloud & Edge Computing
What it means: Cloud and edge computing provide the power and flexibility to handle all the data that digital twins need.
- Cloud platforms (like Azure Digital Twins and AWS Twin Maker) store and process large amounts of data from different sources.
- Edge computing brings data processing closer to where it’s generated (like on factory machines or hospital equipment), which means faster reactions and less lag.
Why it matters: This combo makes digital twins faster, more reliable, and easier to scale without slowing things down.
2. IoT & Sensors
What it means: Digital twins stay accurate because they constantly receive real-time data from connected devices.
- Sensors in machines, vehicles, buildings, or wearables collect information like temperature, motion, or location.
- This data flows directly into the digital twin, keeping it updated and in sync with what’s really happening.
Why it matters: Live sensor data makes digital twins “smart” and always up-to-date, ready to provide useful insights when needed.
3. Artificial Intelligence
What it means: AI and ML help digital twins think ahead and make smart decisions.
- They can predict issues (like when a machine might break) or spot unusual behavior early.
- They also learn from past data to keep improving over time.
Why it matters: This reduces the need for constant human monitoring and allows systems to fix or adjust themselves automatically.
4. Standards & Interoperability
What it means: Digital twins need to talk to many different systems. Standards make that possible.
- Open formats (like DTDL and OPC UA) allow different software, devices, and platforms to work together smoothly.
- Industry groups are also creating shared rules to make adoption easier for everyone.
Why it matters: With shared standards, companies can scale faster, save on integration costs, and connect everything more easily.
5. Visualization & Immersive Technology
What it means: Good visuals help people understand complex digital twins.
- 3D dashboards and real-time visualizations give teams a clear view of what’s happening.
- Tools like AR (Augmented Reality) and VR (Virtual Reality) let users step inside virtual environments, for example, to inspect equipment or practice surgery.
Why it matters: Better visuals mean faster decisions, smoother teamwork, and more effective training especially when people are working remotely or dealing with high-risk tasks.
Conclusion
Digital Twin technology is no longer a futuristic concept. It is a present-day game-changer, revolutionizing industries with its ability to simulate, monitor, and optimize physical systems in real time. This is more than a technological shift—it’s a strategic inflection point.
For savvy investors, Digital Twin presents a rare opportunity to get ahead of the curve. As businesses increasingly embrace data-driven decisions and intelligent automation, the demand for Digital Twin solutions is set to soar. Those who recognize its potential today are not just investing in innovation they are positioning themselves to shape and profit from the industries of tomorrow.
Talk to our experts to learn more.